GRP Staircase: Knowsley Waste Terminal Access
Client: Network Rail
Contractor: Step on Safety Ltd supplied the staircase; installation was conducted by CSM.
Anchor Systems played a key role in the successful installation of a GRP access staircase at the Knowsley Waste Terminal in Merseyside. The 13m long and 5m high staircase was designed to provide safe access between a railway embankment and a cess walkway.
To overcome the challenges of sloped and uneven terrain, the project utilised sixteen galvanised steel Anchor Screw piles, each equipped with two helix plates. Adjustable interface plates allowed for 7° lateral adjustment, ensuring the staircase remained perfectly level. The piles were installed to a depth of 3.60m using portable handheld equipment, enabling a quick and efficient installation process without requiring railway isolations.
Torque monitoring during installation validated the performance of the screw piles, achieving an ultimate geotechnical capacity of 37.9kN. The system met all requirements, including a 100-year design life, offering long-term stability, load capacity, and durability.
This project demonstrates Anchor Systems’ ability to deliver innovative, reliable, and efficient solutions for complex geotechnical challenges, setting a benchmark for quality and performance in the industry.
Read The Full Project Report Here
Anchor Plates and Systems
At Anchor Systems International Ltd, we provide a wide range of high-quality anchoring solutions that use a variety of termination plates in order to meet the unique requirements of your projects.
Our plates are available in bespoke shapes, sizes, and materials, ensuring they can be used for many specific applications across slope stabilisation, retaining walls, heritage conservation, and beyond. Below, you’ll find detailed descriptions of our most popular solutions.
Formed Pattress Plate
Formed Pattress Plates are designed for retaining walls and slope stabilisation, offering a high degree of flexibility in installation angles. These plates are paired with Domed Load Nuts to securely terminate the anchor bar.
Features:
- Bespoke shapes and sizes available.
- High flexibility for angle adjustments.
Applications:
- Retaining walls.
- Slope stabilisation requiring varied installation angles.
Recessed Pattress Plate
The Recessed Pattress Plate is ideal for projects where aesthetics are critical. It offers a flush-finished appearance with hidden terminations, making it perfect for heritage sites and high-traffic areas where safety and appearance are paramount.
Features:
- Flush finish for a clean aesthetic.
- Hidden terminations for safety and design integrity.
Applications:
- Heritage and conservation works.
- Public areas where safety is essential.
Wedge Boss Pattress Plate
The Wedge Boss Pattress Plate provides high load transfer while allowing anchors to be driven at angles of up to 45 degrees. Its flexibility makes it suitable for challenging installations.
Features:
- Supports angled installations up to 45 degrees.
- High load transfer capability.
Applications:
- Complex anchoring projects requiring angled flexibility.
Flat Pattress Plate
Flat Pattress Plates are versatile solutions designed primarily for slope stabilisation where anchors are driven perpendicular to the surface. However, they can also accommodate angled installations when paired with tapered washers. These plates can be secured using either bars with load nuts or wires with barrel and wedge grips.
Features:
- Bespoke shapes and sizes available.
- Compatible with a variety of Vulcan anchor sizes.
- Flexible for angled requirements with tapered washers.
Applications:
- Slope stabilisation projects.
- Infrastructure requiring secure anchoring.
Flat Pattress Plate with Wire
This variant of the Flat Pattress Plate replaces the lock nut with a barrel and wedge grip, allowing for use with wire instead of bar. This design offers additional flexibility for projects requiring different anchoring methods with smaller loads or shorter install depths.
Features:
- Bespoke shapes and sizes available.
- Flexible securing options using wire systems.
Applications:
- Projects requiring adaptable anchoring techniques.
Tapered Washer Pattress Plate
Tapered Washers are used with Flat Pattress Plates for applications requiring flexible installation angles for up to 20 degrees and can support high load capacities.
Features:
- Designed for high-load applications.
- Allows for angled installations when paired with Flat Pattress Plates.
Applications:
- Projects requiring both flexibility and strength.
Combi-Tech Anchor
The Combi-Tech Anchor System is specifically designed for stabilising damaged masonry structures, making it ideal for heritage, listed building renovations, and refurbishment projects. Its concealed top termination preserves the original appearance of structures, ensuring compliance with aesthetic and planning constraints.
Benefits:
- Simple, efficient installation.
- Reduces the need for grout and additional materials.
- High-strength performance.
- Customisable to any length, fitting up to 90mm core holes.
- Testing equipment readily available.
Applications:
- Heritage conservation.
- Masonry stabilisation for historic and listed buildings.
Vulcan Anchor Drain
The Vulcan Anchor Drain system addresses water pressure in slopes or retaining walls through a retro-fit drainage membrane. It utilises a length of Mem?braDrain wicking material secured to the Vulcan anchor head, ensuring immediate drainage and slope stability upon installation.
Features:
- Instantly reduces water pressure and prevents ground saturation.
- Rapid and cost-effective installation.
- Retro-fit solution for embankment stability.
- Finished with mortar pointing or a bespoke plate design.
Applications:
- Road and railway embankments.
- Retaining walls and slope stabilisation.
Benefits:
- Helps prevent embankment failure.
- Relieves puddle pressure.
- Suitable for installation with handheld or machine equipment.
Why Choose Our Solutions?
- Bespoke: All plates and systems can be tailored to your project’s specifications.
- Durable: Manufactured from high-quality materials for long-lasting performance.
- Innovative: Advanced designs ensure safety, flexibility, and efficiency.
- Supportive: Our expert team is ready to assist with technical advice and testing solutions.
Contact Us
Need help choosing the right plate or system for your project? Get in touch with our team today for personalised advice and recommendations. Call us on 01342 719 362 or send us an enquiry via our contact form.
Slope Stabilisation Project - Horsham
Anchor Systems recently completed a slope stabilisation project at Tower Close, Horsham, to address a significant failure that posed risks to a local highway and private property. The project required an innovative approach to restore safety and ensure long-term stability.
Working alongside Ibex Consulting Engineers, we implemented a tailored geotechnical design featuring the Vulcan Earth Anchor, a highly durable and effective ground anchor system. A total of 27 anchors were installed in a diamond formation, complemented by Greenax erosion control mats and anchor drains to prevent hydrostatic pressure build-up. These measures delivered a robust solution, safeguarding the slope for its 120-year design life while protecting the environment.
Completed in just seven days, the project highlights our ability to deliver fast and efficient solutions for complex ground stabilisation challenges.
- Client: Private
- Consultant/Engineer: Ibex Consulting Engineers
- Contractor: Hartmann Construction Ltd
Learn more about this project and how we achieved long-lasting results here
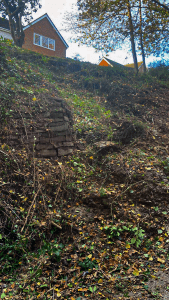
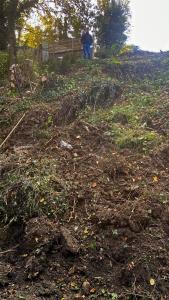
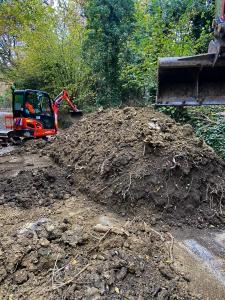
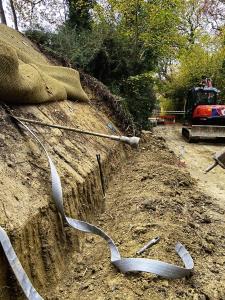
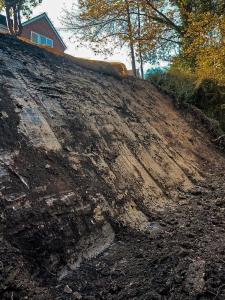
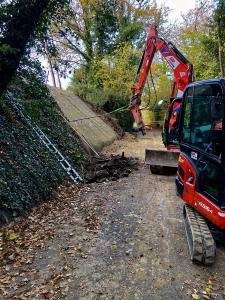
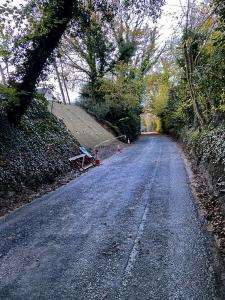
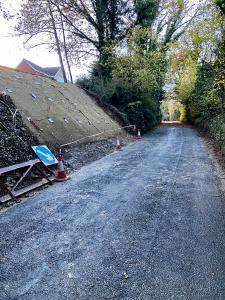
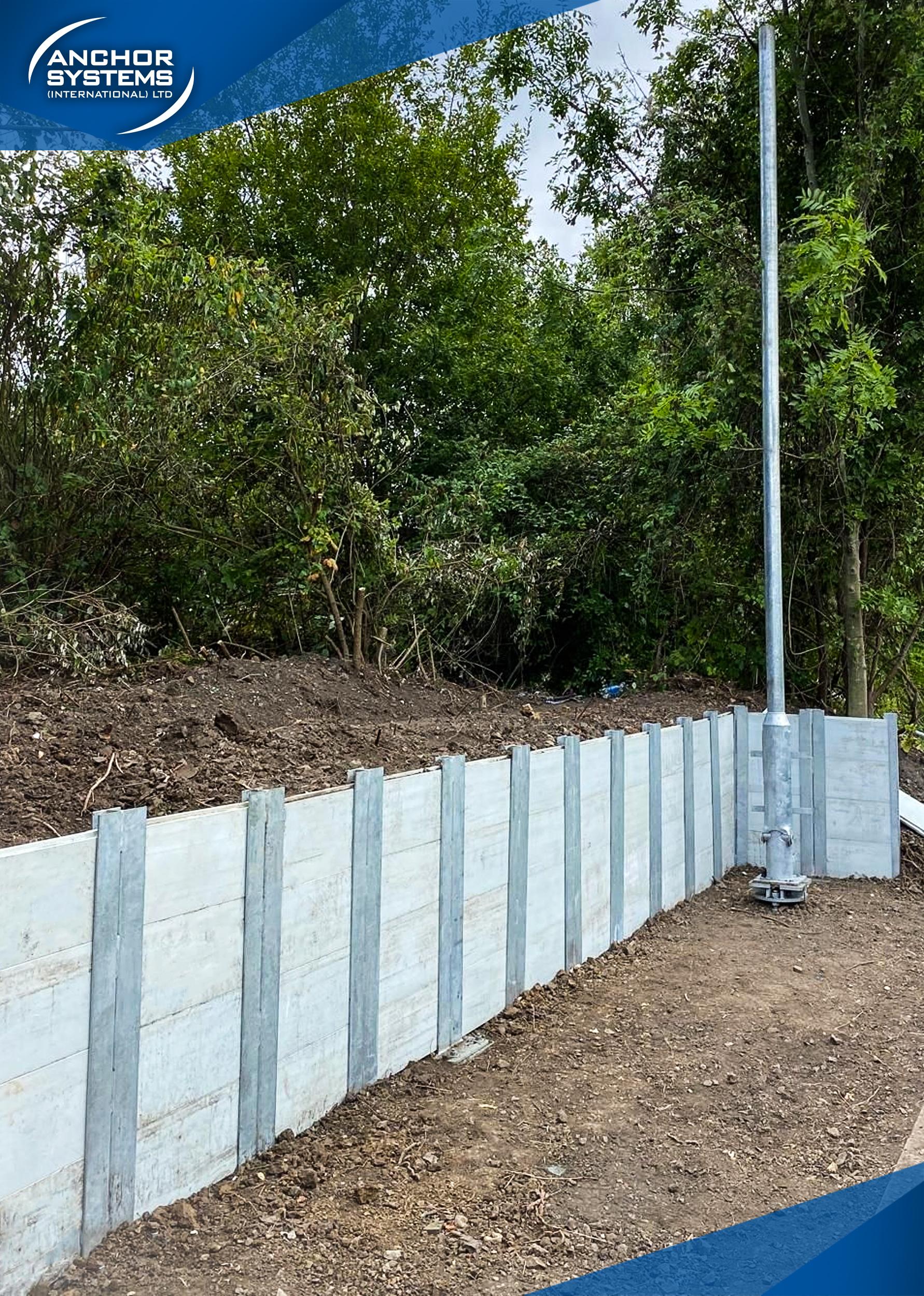
Supporting Sunville Rail’s Innovative 5G Piling Project
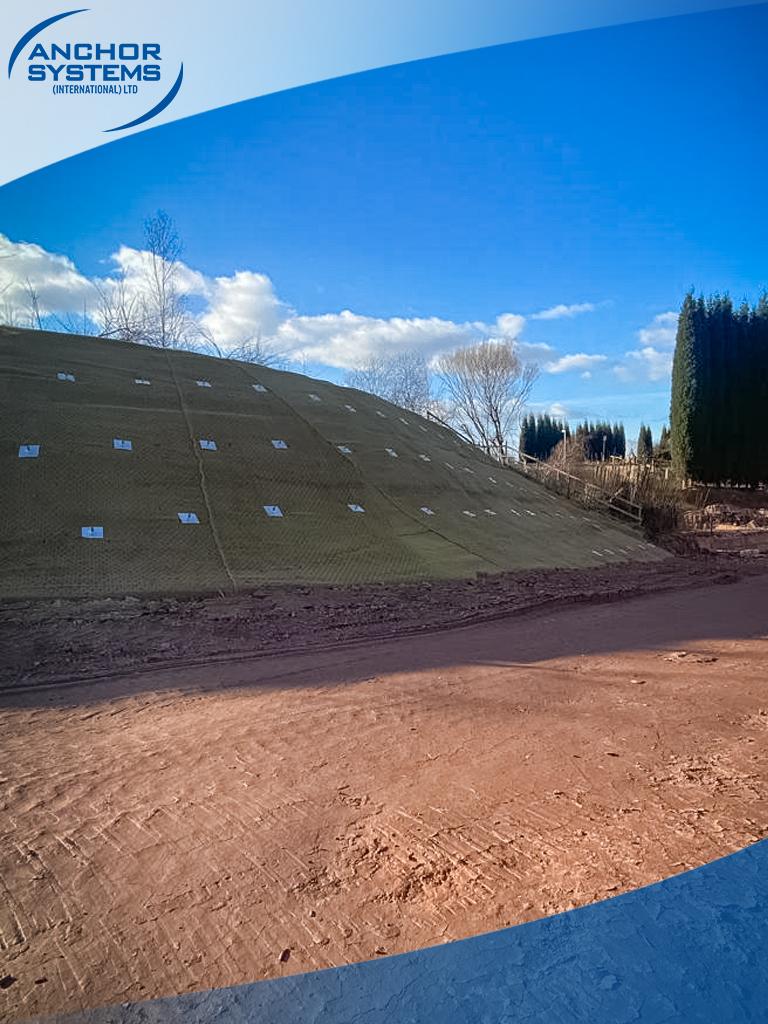
Wilnecote Embankment Support Update
We received some updated images from a project in Tamworth, Staffordshire last year where we aided in tackling a large bund reprofiling works and adding required global stability using our AS-50 Vulcan Anchor system with Greenax Meshing. It’s great to see our Vulcan Earth Anchors thriving in slope stabilisation projects across the UK. ⚓
Click to check out the full project report
[gallery ids="3619,3618,3617"]
Magazine Articles
Anchor Systems (International) Ltd have featured in a number of Rail Professional publications, below are the issues we have featured in this year.
Click on the images to read the relating articles:
In the March issue, you can read about our new Quick-Stage with Anchor Screw foundations used on a Network Rail project in Flitwick, Bedfordshire.
In May’s issue, read about a project where Anchor System’s Vulcan Earth anchors were used to stabilise railway bridge abutments on the A339 in Alton.
In the June issue, read about our new and existing innovative level crossing and trackside systems.
New Hydraulic Power Pack
We have upgraded our range of Hydraulic Power Pack’s to include more benefits for the user.
- Collapsible handle – Making it easy to manoeuvre
- Hinged carry lid – Provides somewhere to carry hoses while still being able to easily access the engine
- UK manufactured engine – Reliable and easily serviceable
- 20-30L – Can be used to install Anchor Posts, Anchor Screws and Vulcan Earth Anchors
- Available to hire or purchase
Download the technical information brochure HERE
[gallery slick_active="true" sl_centermode="true" ids="3169,3170,3171,3172,3173"]
Introducing the Anchor Screw Brochure
Hot off the press and just landed at Anchor Systems HQ is our brand new Anchor Screw brochure! Download it now.
Our patented Anchor Screw is an easy to install foundation solution that has enhanced environmental benefits compared to it’s alternatives.
This system was designed and evolved from the needs of some Network Rail projects that required to improve both the efficiency and sustainability of their standard construction materials and methods.
The Anchor Screw eradicates the need to use concrete and is made in Britain from 100% recycled UK steel. It can also be made with a 100+ year lifespan making it economical as well sustainable.
You can see the system in use in these two project reports:
Hither Green Signalling Renewal Project
Westbourne Park Segregation Barrier Project
Benefits and Features
-
Speed
Typically installed in under 10 minutes per anchor -
Easy to Install
Zero on-track plant or RRV’s required as installed with lightweight, handheld equipment - Dust
Zero dust is generated as no cementitious products required - Environmental
Fully reusable and Made in Britain from UK recycled steel - Longevity
Can be designed with 50 or 100+ year lifespans dependant on client requirements - Water and Drying Times
Zero water consumed or drying time required, as no wet trades involved - HAVS
Zero risk as the installation equipment is non-percussive - Noise
Installation is relatively quiet. The installation equipment runs at 80-85db - Versatility
Easily adjustable to guarantee the correct positioning with patented design features - Mess and Waste Materials
Zero mess due to no digging required nor any general wasted materials, which reduce manhours and project risks
You can download the brochure here: Download Now
Or if you would like to book a CPD presentation for you and your team or get your hands on a physical copy then pop us an email: info@anchorsystems.co.uk
Environmental Case Study with Balfour Beatty
The Challenge
Traditionally, anchorage solutions for backstays use steel sledges with concrete kentledge blocks loaded on to them. This method requires large quantities of concrete blocks to be delivered to the site yard from Balfour Beatty’s Raynesway, Derby stores, then distributed to site using a Man 4×4 wagon with Hiab to install. The maximum number of blocks that can be carried at any one time is 4, meaning several trips are required per location. Additionally, temporary works are required, and Trackway is also needed to get the Man 4×4 to site.
The Measure
Together with the Innovations Team, the project team at ZL Great Missenden OHL pioneered the use of the Vulcan Earth Anchor system (distributed by Anchor Systems International) as an alternative to the traditional method of anchorage. These earth anchors are installed by inserting a drive rod into the anchor driving point and knocking them into the ground. The anchors are driven into the ground by using hand tools or excavators. Ground level anchor plates can be manufactured to the required angle for each individual location as needed.
This innovative alternative meant the reduction of materials used, decreased need for temporary works, removed the need for trakway installation, reduced the construction ecological footprint (for size, setup and delivery) and reduced transport costs. Additionally, the steel drive rods can be removed and reused again. Also recycled wooden pallets are used which are returned to supplier for re-use and the plastic shrink wrap used by Anchor Systems is a Biodegradable wrap.
“Having witnessed the use of this system on site, I found the ease of this installation, very impressive. The logistical reduction and numerous beneficial practicalities speak for themselves and I would like to see the implementation of this system on other schemes where possible”
Andy Robinson, Project Supervisor National Grid.
The Results
- Reduce relative project ecological footprint through reduction in temporary works and removal of required trakway installation (the need for 915m of trakway was mitigated)
- Reduced need for possible trakway ecological mitigations (i.e. trakway sealing for Great Crested Newts/reptiles)
- Delivering a cost saving of £11,849.74 (trackway and transportation costs)
- Material reuse
- Reduced project carbon footprint for backstays from 260,775kg to 7,727kg, for a total saving 253,048kg CO2*
*Calculated using National Grid’s Carbon Interface Tool (CIT)
Download this report HERE
[gallery slick_active="true" sl_centermode="true" ids="2508,2507,2506,2505,2504,2503,2502,2501,2500,2499,2498,2497,2496,2495,2494,2493,2492,2491,2490"]
Are you still using concrete?
Did you know that concrete is the most destructive material on Earth?
It is the most widely used man-made material in existence. It is second only to water as the most-consumed resource on the planet. In an ever-changing world where we are trying to reduce our carbon footprint, we are overlooking one of the biggest causes. Concrete is said to be responsible for around 8% of the world’s CO2 emissions. We have focused largely over the past several years on reducing our plastic use, yet all the plastic produced over the past 60 years amounts to 8bn tonnes, the cement industry pumps out more than that every two years.
We are not saying never use concrete. There is a place for concrete until we find something else that compares with it without the negative impact on the environment. But why use concrete unnecessarily?
When looking at foundation systems, instead of digging up vast areas of earth and filling them with concrete, look at alternatives.
The Anchor Post and Anchor Screw are made up from 100% recycled British steel, do not require any concrete to hold them in place and there is no digging required or removing of the soil. As there is no concrete there is no drying time and installations can be completed in a single visit. The unique dome head allows for adjustments to be made easily and simply. Bespoke interface plates can be designed to suit each individual application.
On a recent project with Balfour Beatty and Network Rail (see here), our system was used instead of concrete and the below results were recorded:
- 60 per cent time saving on foundation installation
- 40 per cent cost saving of £369 per metre to £221 per metre (derived from man hour savings, elimination of plant requirements, reduced possession requirements)
- 73 per cent embodied carbon reduction on materials, equivalent to 13,920kg CO2e and 89.4 per cent material saving
- Zero on-track plant and zero water consumed
- UK manufacturing and local materials, eliminating mainland European transportation miles
If you would like to find out more about the Anchor Post or Anchor Screw and how it can eradicate the need for concrete and make your next project a more sustainable one, then please email us or contact us on 01342 719 362.
You can also download our brochures here.
Sources:
https://www.bbc.co.uk/news/science-environment-46455844
https://www.theguardian.com/cities/2019/feb/25/concrete-the-most-destructive-material-on-earth